Began with putting a brand new Airtex 60577 on. The bolt holes are through and through the block wall, making it necessary to put some thread sealer on the bolts so that oil doesn't migrate out along the threads - something that coarse threads are more than willing to allow. I doped up the cam lobe with some Lucas Assembly Lube before installation.
To its credit, the old pump was still pumping, but for how long? I figure it would conk out just as I was getting everything going well and I really hate to be disappointed in that way. Soooo...new pump it is!
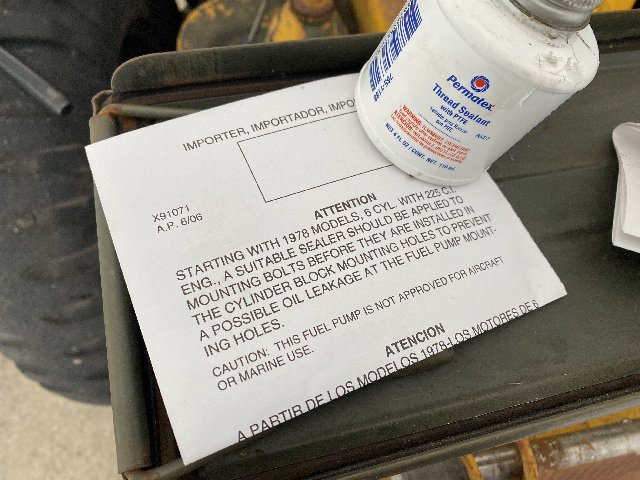
One step forward.
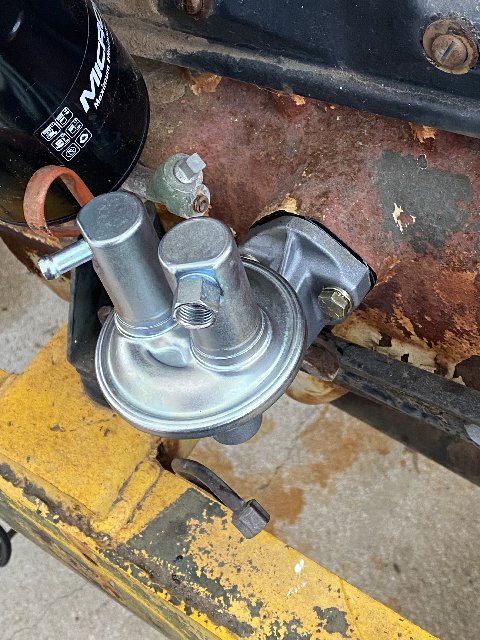
Decided to clean up the face and the hub of the shaft of the water pump. It was quite a chore getting that pulley off due to rust build-up on the hub of the shaft. So, with this cleaned up and the inner face of the pulley cleaned up things should come back together just a bit more nicely when it comes time.
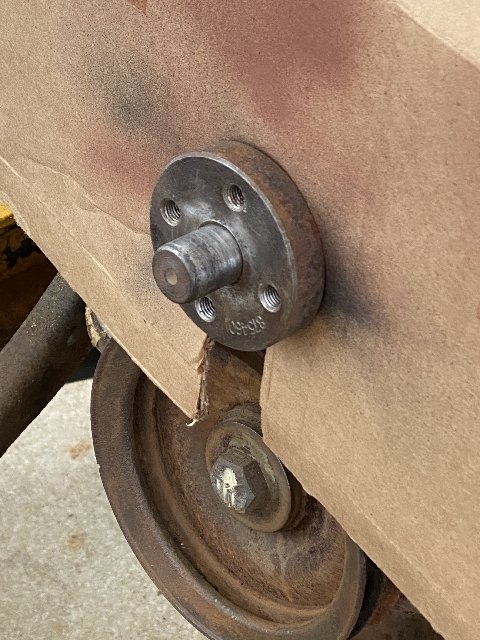
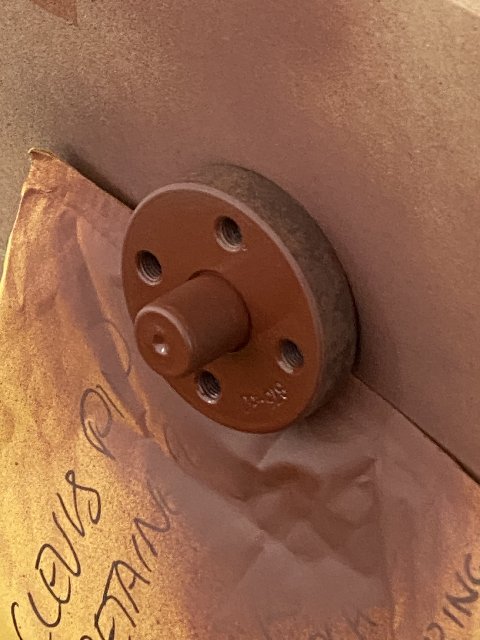
After cleaning up the fan a close inspection revealed a crack. One step back. Doggone it! But, the good news is, that pretty radiator isn't going to be chewed up by a fan blade coming off so there is a little ray of sunshine with this discovery.
I actually took a stab at drilling down through the outer blade centering my holes at the crack and then welding these new holes up, rejoining both sides of the crack as well as the front blade to the back blade.... Not a bad idea but, after I put the wire wheel to it to clean it up, I could see that the crack had progressed, in two directions, far further than I could see in this picture. That crack is gonna go where that crack is gonna go and I won't be able to see it when everything is reassembled so, I'm simply not going to risk it.
This fan going to the scrapper where it can never, ever harm anyone again....probably with a big bend in it just to make sure somebody doesn't try to reuse it.
Yet another disaster neatly side-stepped and one brand new fan blade on the way.
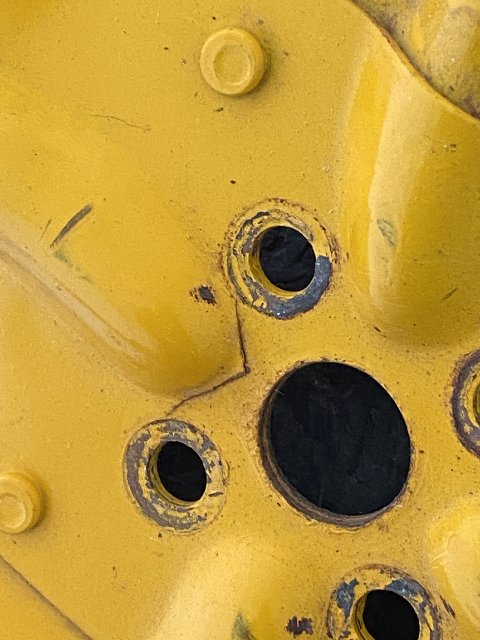
Made a trip to Tractor Supply for some new hardware. Getting things organized. A brand new bushing for the top of the radiator and new everything for the bottom. (yeah, I know....there's extra hardware in there)
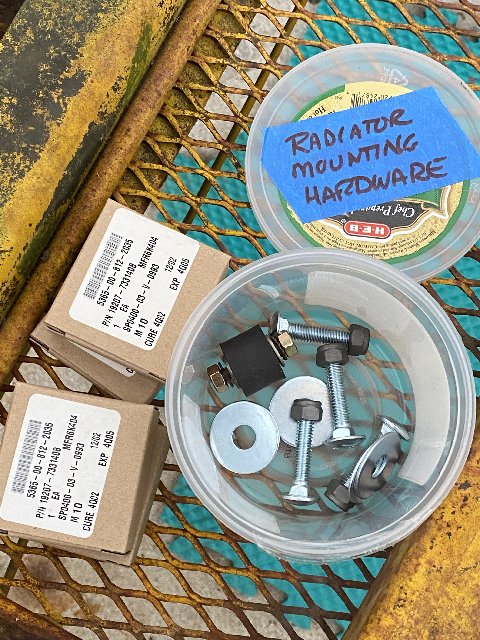
And look what I found at Tractor Supply! inner diameter of the ring eye is 5/8". Inner diameter of the bushing is 1/4". These will need to be drilled out to accomodate a metal sleeve through which will pass the mounting bolt. This is my favorite option thus far and happily, it isn't going to be a lot of work. Best of both worlds.
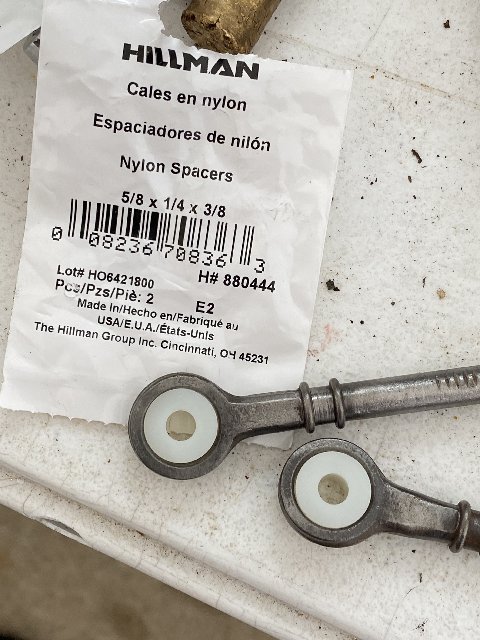
As you can see here, the original bushings are surprisingly thin, even when brand new.
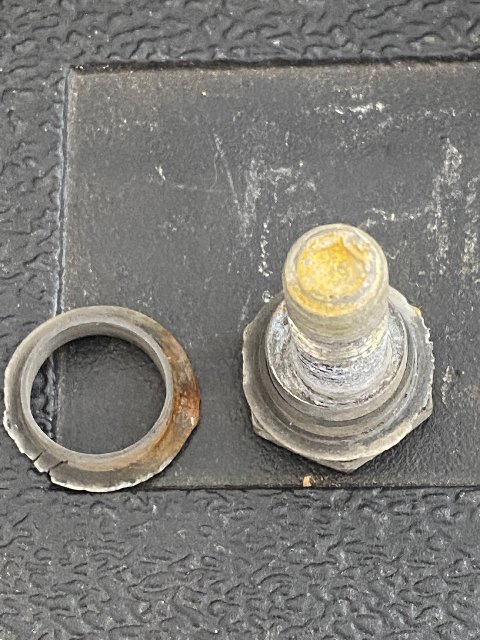
In this second option, these bushings would have to be thinned down to accommodate the eccentric lobe on the original mounting bolt. As I mentioned before, in this application the eccentric is not needed and I like the idea of having a bit more bushing in there (as is provided in Option #1, above) especially since all of this is kind of farm-boy engineering and everything is half a bubble off plumb.
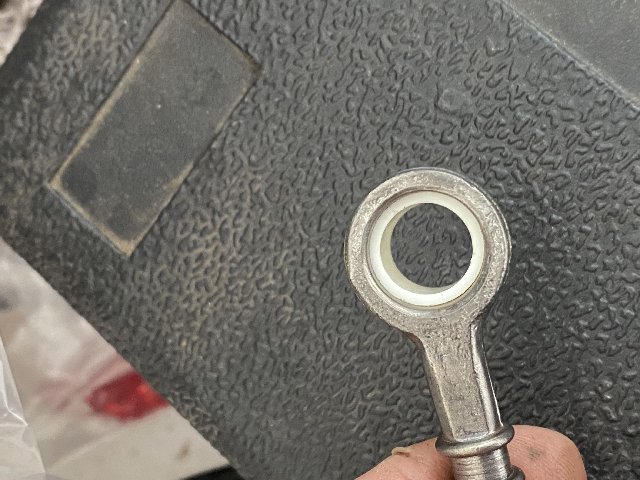
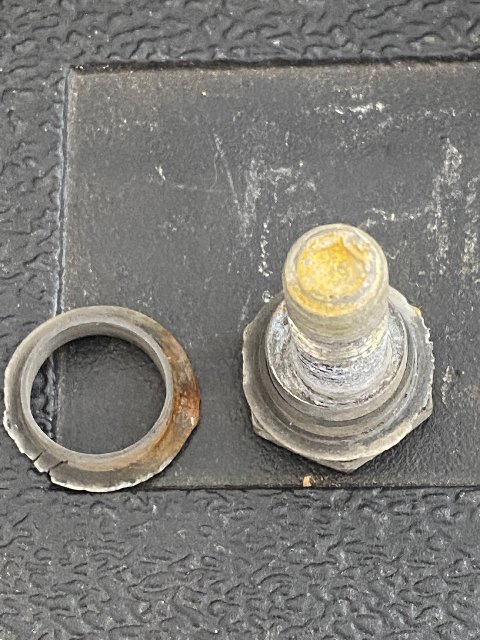
Lots of new hardware and other goodies staged where I can't forget them. I have a lot going on all at once and no particular continuity going on any one part of this project, largely due to parts that haven't arrived or parts that have been painted and are still drying. Doing this helps me stay better organized.
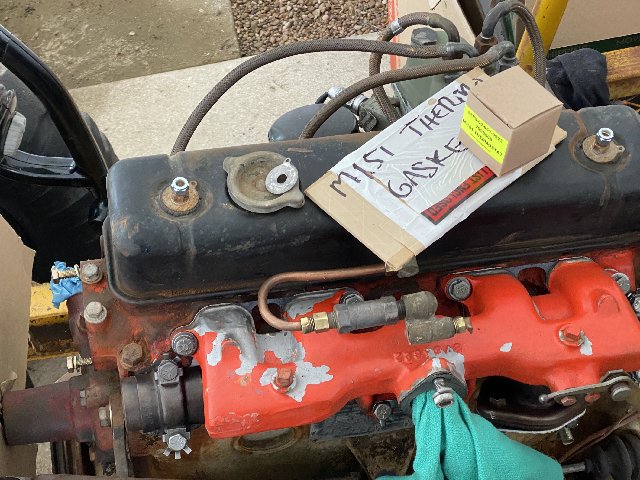
This pulley gets a makeover inside and out. The grooves and the inside mounting face had a lot of rust. I didn't like the idea of huge chunks of rust making my new matched set of V-belts into an old matched set of V-belts in a mere 10 minutes of run time. Not perfect, but pretty good... Far better than it was.
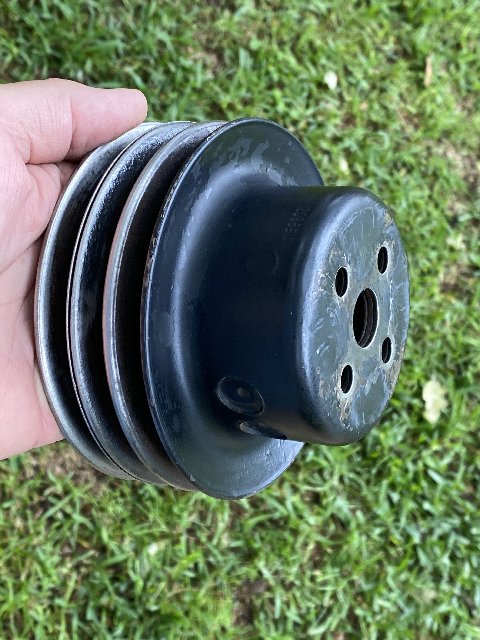
Now to the issue of driveshaft phase. I'm not an expert on the matter but this link explains it pretty well and by the way, KUDOS to Rick for bringing the matter up in the first place. Thank you Rick!
https://www.youtube.com/watch?v=Idk3BVDVHq4
In the case of the Doom Buggy, we are using a FRONT suspension in the rear and the rear output shaft on the transmission is very much in-line with the input of the rear differential. If I recall correctly, the general rule for vehicles with differentials that travel up and down is - having some angle is good, provided those angles are the same at both ends of the shaft but a dead-straight line between output and input are the devil's own playground. But this is a vehicle where the output and input are fixed in place and probably only a few degrees out of line so maybe, just maybe we can get away with a few little irregularities. Doubtful, but you never know.
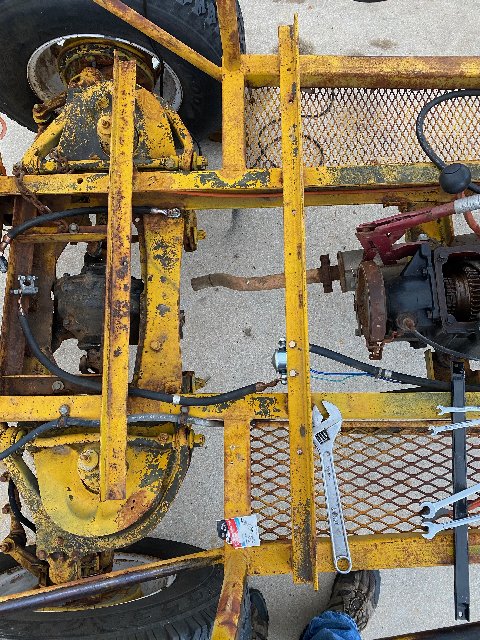
When they built the rear drive shaft for the Doom Buggy (as Rick put it, "there was probably beer involved") they took what was originally a front drive shaft, cut it down and replicated the 1/4-turn-out-of-phase configuration without giving much consideration to where this drive shaft was going to serve. 1/4-turn-out-of-phase would be entirely correct for a stock M151 front drive shaft. This 'error' MAY be why this came to me with the rear drive shaft out of the truck. Between the wheels being off center on the hubs and the rear shaft yammering away, this might have been a really interesting ride, eh?
All that said, what I intend to do is put it back together and see how it behaves. If it's wonky, well, it's not like it's hard to get to! I'll pull it back out and make some changes. We'll get it sorted. I can promise you that.... No dramas.
Now, for a moment, let's revisit the issue of the clutch and brake pedals and the limits to the available free space around them. The most pressing issue at the moment is having space for one's feet so as to be able to operate these pedals independently of one another..
(Photo below) - The vertical tube in the top right corner of the photo is the A pillar. It terminates at a horizontal member that forms the driver's side of the cockpit. Presently, a forward continuation of the horizontal member is a turn-down which terminates at the top of the sponson frame. It is a mirror of the one on the right side of the vehicle. The real fly in the ointment is the location of that turn-down tube because it really intrudes into the space one needs to get on that clutch pedal (and be able to do it without having to look at it to be sure one is not also on the brake). The turn down tube causes the driver's foot to have to be too far to the right which, in turn, leaves part of the driver's foot on the brake pedal as well. Which is very disconcerting when there are lots of other things going on.
I'm quickly coming to the conclusion that the turn-down tube on the driver's side needs to be removed altogether and a linear continuation of the A pillar be installed in the form of a tube going almost straight down to the frame of the sponson. The strength of the roll cage would certainly benefit from it. Some gussets wouldn't hurt either but I'm not going to be driving it in that way so for now it is what it is.
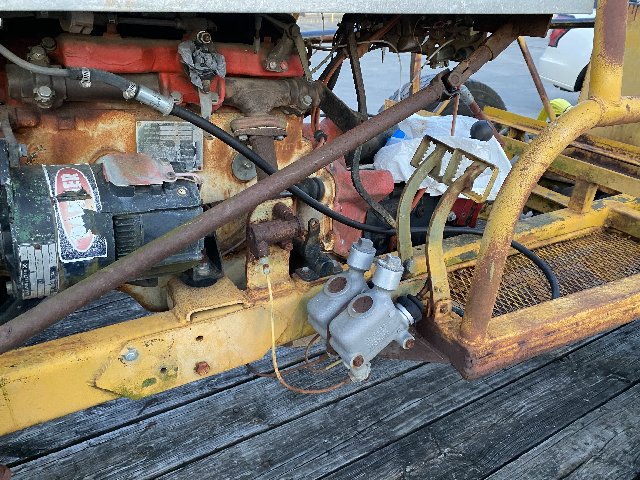
Developing some additional protection for the driver's feet is on the to-do list as well.
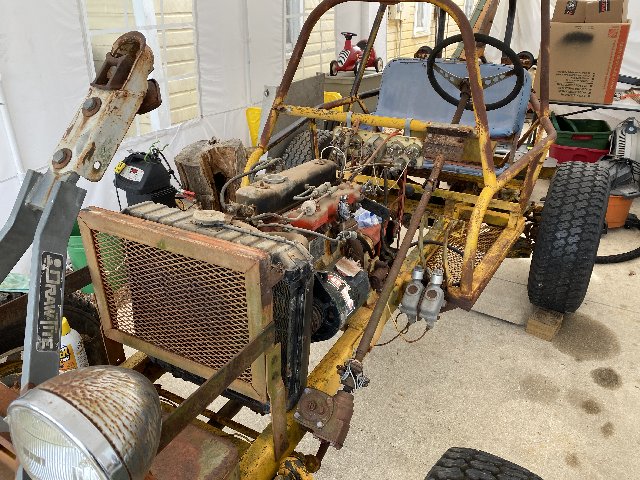
More mechanical mayhem tomorrow!
Cheers,
TJ